摩擦圧接とは
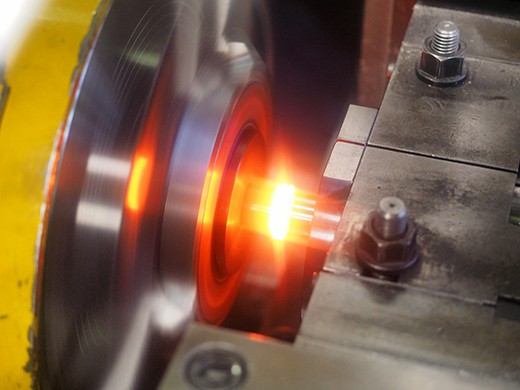
摩擦圧接とは、2つのワークをこすり合わせて発生させた摩擦熱により、ワーク(部材)を軟化させ、同時に圧力を加えることで接合する工法です。接触面の酸化膜層が摩擦カールとして外部に押し出されるため、完全無酸化面が原子レベルで接合します。
生産性が高く、溶接と差別化される特徴があります。
使い方次第で大きなメリットを得られる可能性が御座います。
・接合面が全面接合(母材同等の強度)
・異材種の接合が得意
反面、下記弱みもある点は注意が必要です。御相談下さい。
① 摩擦カール 接合後に必ず生じます。外径は必要に応じて除去が可能ですが、パイプ材の場合、内外径ともに生じるため、内径の摩擦カールは除去出来ないケースが生じます。
②対応能力 特殊な加工のため、設備による対応可能寸法レンジが狭い。またメカニズム上、摩擦熱を発生させづらい小径は苦手。
摩擦圧接のポイント・メリット
01. 高強度化 (溶接→摩擦圧接)
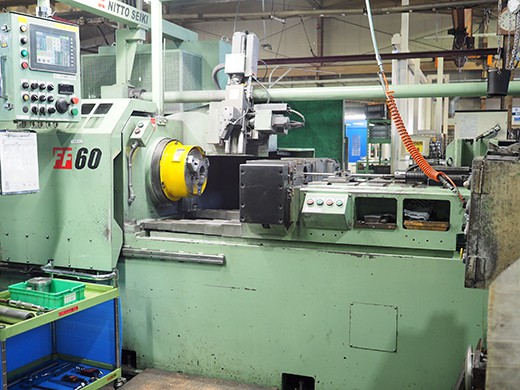
Φ30のシャフトを溶接した場合、折角のシャフト強度も実際は溶接ビードでしか接合しておらず、パイプ強度になってしまいます。
摩擦圧接なら接合部は全面接合。母材同等の強度を得ることが出来ます。強度改善でお困りの際は、一度御検討下さい。
02. 高精度化、軽量化 (「圧入+溶接」→「摩擦圧接+仕上加工」)
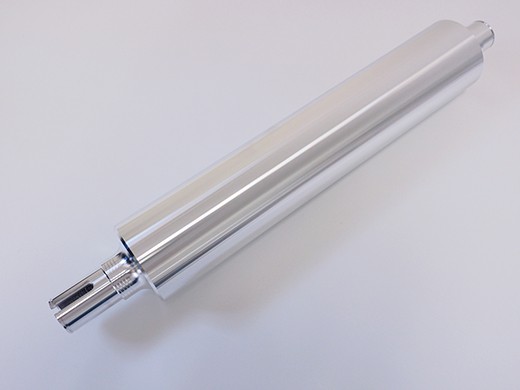
ローラ胴部にボス(フランジ)を圧入、もしくはその後に溶接まで実施する構成を良く見かけます。両端のボスに対してローラ胴部のフレ精度が求められますが、インロー部の内外径公差や同軸精度などが厳しく求められ、それでも圧入&溶接で精度が出せず、最後は手作業で修正。こんな経験ありませんか?
摩擦圧接を使用すれば、素材の段階でローラとボスを接合。接合部は全面で接合しているため、後加工が可能。接合後に加工仕上することで機械精度レベルのフレ精度を安定的に得ることが出来ます(弊社実績:0.03)。
また、ローラ胴部を中空にしてフランジを摩擦圧接することで、中空ローラを作成可能。部品の軽量化が可能です。
03. 省スペース化、少部品化 (「適材適所」「機能の集約化」)
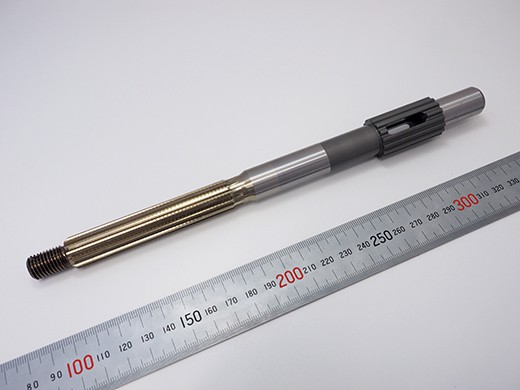
部品の材質は使用環境や目的によって決定されます。
(耐食→ステンレス、強度→焼入れ鋼(SC材、SCM材、など))
これをつなぐ為には「継ぎ手(ジョイント)」が必要になり、この位置関係を調整するための調整機構が必要になります(実際には更にそれぞれの部品を保持するための軸受けやシール部材なども必要なケースあり)。
摩擦圧接を活用することで、これらの機能を集約した部品を作成することが可能です。これを「適材適所」「機能の集約化」と呼んでいます。
必要な箇所に必要な材質を適用した「異材質接合部品」を作成。接合後の仕上加工により必要精度も確保。この部品を使用することにより、「継ぎ手不要」「調整機構廃止」を達成。劇的な省スペース、少部品化を成立させる可能性を産み出します。
なお、この改善は設計段階での適用が必須です。
開発初期段階で御相談頂けると幸いです。